How does the design of the extruder barrel screw impact the overall efficiency and output of the extrusion process?
The design of the extruder barrel screw plays a crucial role in determining the overall efficiency and output of the extrusion process. Here are several key aspects to consider:
Melting and Mixing Capability: The extruder barrel screw's design intricacies profoundly impact the thermal dynamics within the extrusion process. In a comprehensive design, the channel depth, helix angle, and flight geometry are meticulously tailored to ensure an optimal balance between material residence time and the application of thermal energy. This precision facilitates not only efficient melting but also a thorough mixing of components, yielding a homogenous melt crucial for achieving consistent material properties and end-product quality.
Throughput and Production Rate: Beyond basic geometric parameters, the extruder barrel screw's pitch, diameter, and length are meticulously calculated to govern material flow dynamics. A well-optimized screw profile minimizes material stagnation and backflow, promoting a continuous, even flow. This seamless material transport, in turn, boosts throughput and production rates, enabling the extruder to handle larger volumes while upholding the desired quality standards of the extruded product.
Pressure Build-Up and Venting: Pressure management is a delicate orchestration in extrusion, and the extruder barrel screw's design is paramount in orchestrating this balance. Intelligently integrated venting zones, variable channel depths, and precise pressure control mechanisms work in concert to mitigate pressure build-up issues. This not only prevents material degradation but also safeguards against extrusion irregularities, ensuring a stable and reliable production environment.
Energy Efficiency: The screw's impact on energy efficiency extends beyond geometric considerations. Advanced designs incorporate elements such as optimized shear profiles and enhanced material flow characteristics to minimize internal friction, reducing the energy required for extrusion. Furthermore, cutting-edge features like energy-efficient motor drives and specialized screw coatings synergistically contribute to overall energy conservation, aligning with modern sustainability and cost-effectiveness goals.
Material Conveyance and Compression Ratio: A nuanced understanding of material rheology informs the extruder barrel screw's flight configuration and compression ratio. Striking a delicate balance, the design facilitates efficient material conveyance while ensuring judicious compression, preventing over-shearing or over-compression-induced degradation. This tailored approach is fundamental in achieving optimal material densification without compromising the inherent properties of the processed material.
Temperature Control: Precision in temperature control is meticulously embedded in the extruder barrel screw's design through strategic placement of cooling channels and heating elements. These features work cohesively to maintain a consistent thermal profile along the extruder barrel. The result is a controlled and uniform temperature distribution throughout the material, preventing localized overheating or cooling and guaranteeing the repeatability of material properties across production batches.
Wear Resistance and Longevity: The extruder barrel screw's material composition and surface coatings are judiciously selected to withstand the harsh conditions of extrusion. High resistance to abrasion and corrosion is ensured, significantly enhancing the wear resistance of the screw. This meticulous material selection and coating application contribute synergistically to extend the lifespan of the extruder equipment, reducing downtime and maintenance costs, thereby optimizing overall operational efficiency.
Adaptability to Materials: The adaptability of an extruder barrel screw to a diverse range of materials is a testament to its comprehensive design. Beyond geometric considerations, the screw is engineered to accommodate the varying rheological properties of different polymers, compounds, or formulations. This versatility empowers the extrusion process to seamlessly transition between materials, enhancing the overall flexibility and utility of the equipment across diverse production scenarios.
Film blowing screw mixing head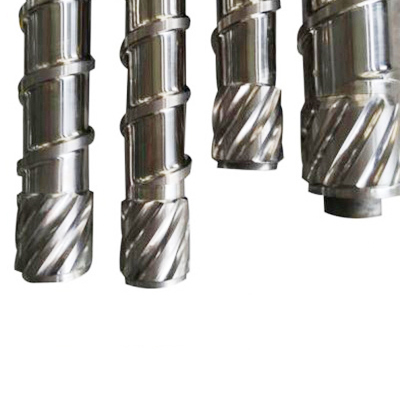