What are the challenges faced in balancing the rotational speed and torque requirements of a high-speed double mixing extruder screw?
Balancing the rotational speed and torque requirements of a high-speed double mixing extruder screw is crucial for achieving optimal performance and efficiency in the extrusion process. Several challenges are faced in this regard:
1.Heat Generation:
High rotational speeds in extruder screws result in increased friction between the screw and the processed material. This friction generates heat, which can lead to thermal degradation of the material. Balancing the rotational speed is critical to prevent excessive heat buildup and maintain the material's integrity and desired properties.
2.Material Viscosity:
Materials processed in high-speed extruders often vary widely in viscosity. Balancing rotational speed and torque becomes challenging when dealing with materials that have significantly different flow characteristics. Understanding the rheological behavior of each material is essential for determining suitable operational parameters.
3.Shear Rate:
The shear rate, a measure of how quickly adjacent layers of material move with respect to each other, increases with higher rotational speeds. Excessive shear rates can degrade the material, altering its molecular structure and resulting in poor product quality. Balancing the speed is crucial to maintaining an optimal shear rate that ensures thorough mixing without causing degradation.
4.Torque Requirements:
Extrusion processes require higher torque to overcome the resistance caused by the material's viscosity and the pressure developed during extrusion. Balancing the rotational speed with the necessary torque is essential to prevent overloading the motor and associated drive components. Proper matching of speed and torque ensures efficient power utilization and prolongs the lifespan of the equipment.
5.Screw Design Complexity:
High-speed double mixing extruder screws often feature intricate designs, including multiple flight profiles, pitches, and mixing elements. Achieving the right balance between speed and torque is challenging due to the complexity of these screw designs. Engineers must carefully analyze the screw geometry to optimize both parameters for efficient processing.
6.Wear and Tear:
High rotational speeds accelerate wear on the screw and other components, leading to increased maintenance requirements. Balancing the speed is essential to mitigate wear and tear, ensuring longer equipment life and minimizing downtime. Proper maintenance practices, including regular inspections and component replacements, are vital for addressing wear-related challenges.
7.Dynamic Response:
The extruder system's dynamic response, referring to its ability to adapt to changes in speed and torque, is crucial for stable operation. Rapid adjustments in rotational speed and torque are necessary to maintain consistent processing conditions. Balancing these parameters while ensuring a stable dynamic response is essential for preventing system instabilities, such as vibrations or material surges.
8.Material Flow Consistency:
Inconsistent rotational speeds or torque can lead to uneven material flow within the extruder barrel. Non-uniform material flow results in product defects, affecting product quality and consistency. Balancing speed and torque parameters is essential to ensure consistent material flow, enabling the production of high-quality extruded products.
9.Process Control:
Achieving precise control over rotational speed and torque requires advanced control systems integrated into the extrusion process. These systems use sensors and feedback mechanisms to monitor the process variables continuously. Real-time data analysis and control algorithms enable quick and accurate adjustments, ensuring the extruder operates within the desired speed and torque ranges.
10.Energy Efficiency:
Balancing speed and torque is fundamental to optimizing the energy efficiency of the extrusion process. Running the extruder at the right speed and torque levels minimizes energy consumption while maintaining the required production rates. Energy-efficient operation not only reduces operational costs but also contributes to sustainable manufacturing practices.
High speed double mixing extruder screw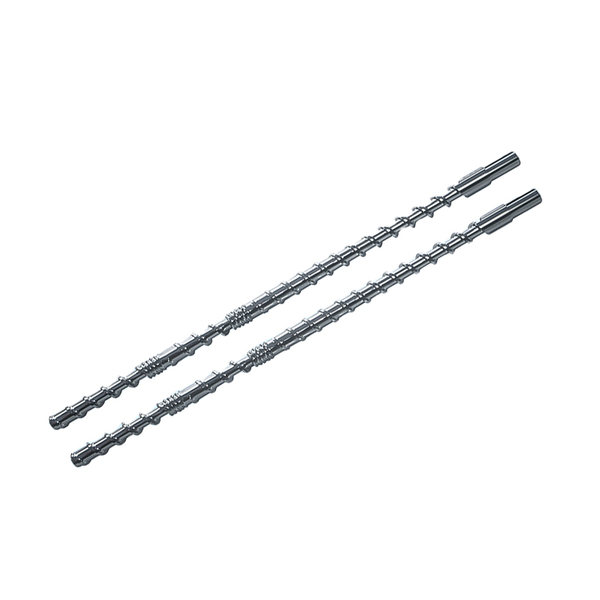