What are the key advantages of using a parallel twin screw barrel in comparison to other types of screw configurations?
Parallel twin screw barrels offer several advantages compared to other types of screw configurations, especially in the context of extrusion processes. Here are some key advantages:
Enhanced Mixing and Homogeneity: The dual-screw configuration of parallel twin screw barrels promotes an expansive intermolecular interaction surface, fostering both distributive and dispersive mixing. This intricate mixing mechanism ensures an unparalleled level of homogeneity in the melt phase. This feature is particularly crucial in applications where consistent material composition is paramount for achieving precise product specifications and quality standards.
Increased Throughput: Parallel twin screw extruders exhibit an exceptional capacity for processing significantly larger material volumes within a given timeframe. This heightened throughput is a direct result of the simultaneous and synergistic action of the parallel screws. Industries with demanding production schedules benefit immensely from the accelerated material processing rates provided by parallel twin screw configurations, translating to increased efficiency and reduced manufacturing timelines.
Versatility in Processing Various Materials: The inherent adaptability of parallel twin screw extruders positions them as the workhorse across a vast spectrum of materials. From low-viscosity polymers to high-filler-content compounds, the parallel twin screw design accommodates a diverse array of formulations. This versatility renders these extruders indispensable across industries requiring the processing of materials with varying rheological properties, allowing for a single extruder to handle a multitude of material types.
Temperature Control: Precision in temperature control is a defining characteristic of parallel twin screw extrusion. The unique ability to independently manipulate the speed of each screw allows for meticulous adjustment of residence time, shear rates, and temperature profiles. This level of control is particularly advantageous in applications where maintaining a specific processing temperature is critical for achieving optimal material properties and ensuring the highest quality end products.
Improved Conveying and Self-Wiping Action: The closely intermeshing screws in parallel twin screw barrels facilitate seamless material conveyance along the entire length of the extruder. This, combined with the self-wiping action between the screws, serves as a robust mechanism to minimize the risk of material stagnation or degradation. This feature is especially advantageous in scenarios involving challenging materials prone to sticking or causing wear on conventional extruder designs, ensuring a consistent material flow and preventing quality issues.
Reduced Shear Heating: Parallel twin screw barrels are engineered to mitigate excessive shear heating, a common concern in extrusion processes. This becomes particularly crucial when dealing with shear-sensitive materials. By minimizing shear-induced temperature spikes, parallel twin screw extruders preserve the molecular integrity of materials, resulting in a final product with superior mechanical and thermal properties. This feature is pivotal in ensuring the production of high-quality materials without compromising their structural integrity.
Flexible Processing Conditions: The independent control of screw speeds in parallel twin screw extruders provides operators with an unparalleled level of flexibility in tailoring processing conditions. Whether adjusting shear rates for enhanced mixing or optimizing residence times for specific reactions, this adaptability ensures optimal performance across a diverse range of applications. The extruder becomes a highly customizable tool, allowing for precise control over processing parameters to meet the unique requirements of different materials.
Compact Design: Parallel twin screw extruders, with their inherently compact design, represent a paradigm of efficiency in space utilization. This becomes particularly advantageous in facilities where spatial constraints are a consideration. The efficient use of space not only contributes to a more organized and streamlined production environment but also allows for greater flexibility in equipment layout and integration within existing manufacturing setups.
WEBER 107MM Flat Twin Screw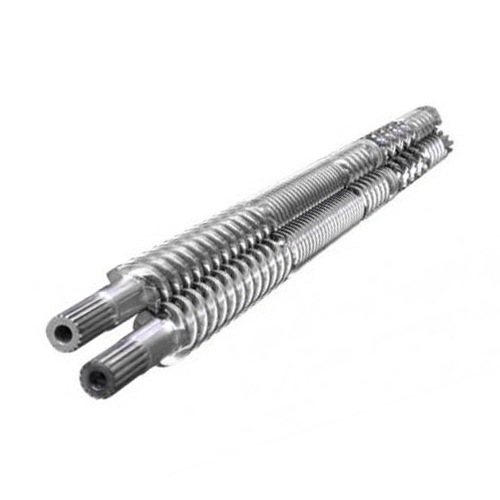