What are the key factors influencing the decision to use a single or multi-layer double-pipe die configuration?
The decision to use a single or multi-layer double-pipe die configuration in extrusion processes depends on various factors, including:
Product Requirements: The choice between a single or multi-layer double-pipe die configuration is inexorably tied to the unique demands of the end product. Whether it involves achieving micron-level precision in layer thickness, intricate variations in material composition, or highly specific structural features, the die configuration must serve as a finely tuned instrument to meet the exacting specifications of the final extrudate.
Material Compatibility: The compatibility of materials assumes a paramount role, especially in applications where the synthesis of disparate materials is imperative. A multi-layer configuration not only permits but strategically exploits the potential to introduce a diverse array of materials into distinct layers, enabling the creation of a composite extrudate with tailored and synergistic material properties.
Cost Considerations: The financial battleground intensifies as we scrutinize the multifaceted costs associated with die configuration. Beyond the upfront costs of design and fabrication, the analysis extends to the ongoing operational expenses and the meticulous calculus of long-term maintenance. A judicious cost-benefit analysis becomes indispensable, weighing the perceived advantages of a multi-layer configuration against the economic realities.
Process Flexibility: In the dynamic realm of manufacturing, characterized by ever-evolving market dynamics and fickle consumer demands, process flexibility emerges as a strategic imperative. The adaptability inherent in a multi-layer die configuration, allowing real-time adjustments to layer composition and characteristics, positions manufacturers to navigate the unpredictable currents of the market with agility and responsiveness.
Extrusion Speed and Throughput: The relentless pursuit of operational excellence brings the focus to extrusion speed and throughput. Here, the multi-layer die configuration takes on the role of a performance amplifier, potentially unlocking higher production rates and, consequently, elevated operational efficiency. It becomes a calculated bet on maximizing throughput in scenarios where rapid and high-volume extrusion is a linchpin of success.
Die Design Complexity: The battleground of design complexity demands a nuanced strategy. A multi-layer die, adorned with intricacies from its geometric design to its internal channel architecture, necessitates a sophisticated engineering approach. The decision to embrace this complexity is a strategic one, balancing the potential benefits of a multi-layer configuration against the challenges inherent in navigating the labyrinth of design intricacies.
Quality and Uniformity: The unyielding pursuit of excellence extends to product quality and uniformity, where the multi-layer die configuration emerges as a maestro orchestrating precision. Its ability to exert meticulous control over layer characteristics becomes the linchpin for achieving the exacting standards demanded by industries where uniformity is not just a preference but a non-negotiable prerequisite.
Material Savings: The crossroads of sustainability and economic prudence intersect in the consideration of material savings. A multi-layer die, acting as a steward of resources, allows for the strategic use of thinner layers or the incorporation of recycled materials in specific strata. This alignment with broader industry trends underscores a commitment to both eco-friendly practices and economic frugality.
Compatibility with Downstream Processes: The strategic alignment extends beyond the die's confines to its seamless integration with downstream processes. The chosen die configuration must not only produce an extrudate of exquisite quality but must also synchronize harmoniously with subsequent manufacturing steps, avoiding bottlenecks and ensuring a continuous and efficient production workflow.
Double-pipe Die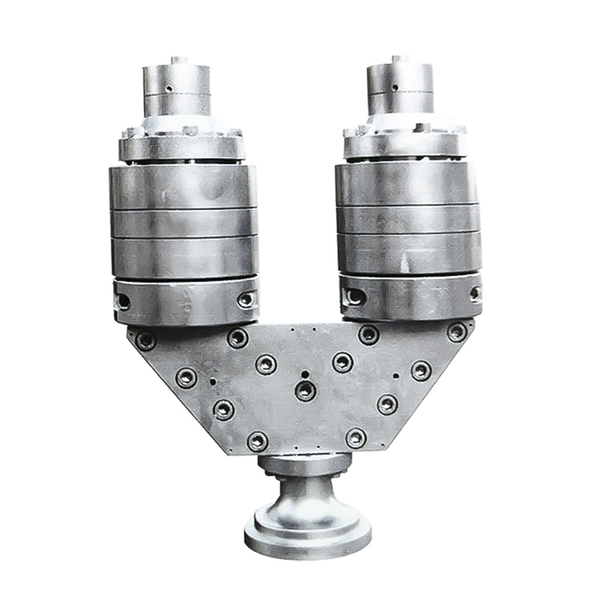